top of page
PROJECTS
Balerion Development Engine
BALERION DEVELOPMENT ENGINE
October 2017 - October 2019
Balerion is the largest student-built, additively manufactured, bi-propellant, pressure-fed, liquid rocket engine designed by students at the Liquid Propulsion Laboratory (LPL) at the University of Southern California (USC). The engine was developed to test the capabilities of additive manufacturing in correlation to features such as regenerative cooling, film cooling, and pintle injection.
UPDATE: During Static-Fire 1, an anomaly occurred at start-up which caused immediate flange separation and resulted in a flame propagating radially out of the engine. After the post-fire analysis, multiple failure points were discovered and a conclusion as to the primary cause could not be drawn based on the data available. However, all lessons learned and probable causes were recorded for the team working towards Static-Fire 2.
Balerion Static-Fire 1
Play Video
Balerion Development Engine Static-Fire 1 (6 seconds) at the Reaction Research Society (RRS) in Mojave, California on September 29, 2019
Nominal Engine Parameters
Propellants
Chamber Pressure
O/F Ratio
LOX/Kerosene
2.59 MPa (375 psia)
1.5
Chamber Temperature
Thrust
Specific Impulse
2464 K (3976 °F)
10 kN (2248 lbf)
241 s
Total Mass Flow Rate
4.25 kg/s (9.37 lbm/s)
Personal Responsibilities:
-
Concept design
-
Pintle injector sizing
-
NX modeling (Full Engine)
-
GD&T drawing package (Full Engine)
-
Oversaw printing and machining
-
Post-processing with outsourcing firms
-
Engine assembly
-
Task delegation
-
Team management
-
Project schedule / deadlines
-
Budgetary needs / funding allocations
-
Coordination with UCSD SEDS to secure a test stand capable of static firing Balerion
-
Test procedures
-
Data analysis
-
Technical writing / publications
-
Test conductor at cold flows and static fire
For detailed information on the engine design or my leadership capabilities, please follow the links below.
Hydra Test Stand / J&J Engines
HYDRA TEST STAND / J&J ENGINES
September 2017 - October 2019
Hydra is the Liquid Propulsion Laboratory's (LPL) in-house test stand capable of firing GOX/Kerosene rocket engines. Jessie & James (J&J) are modular additively manufactured workhorse engines designed specifically around Hydra to allow for rapid prototyping and testing of various performance parameters (i.e. injectors, throttling, etc.). These tools serve as a foundation for LPL to train members on the systematic approach to designing, manufacturing, testing, and static-firing liquid rocket engines. The current focus is on characterizing the Jessie engine using Hydra to validate performance specifications.
UPDATE: Since Static-Fire 3, LPL has iterated upon Hydra to increase its performance capabilities and reliability. In Spring 2021, LPL successfully conducted Static-Fire 4 and recorded all performance data.
Nominal Engine Parameters
Propellants
Chamber Pressure
O/F Ratio
GOX/Kerosene
6.895 MPa (1000 psia)
1.875
Chamber Temperature
Thrust
Specific Impulse
3266 K (5418 °F)
3.32 kN (750 lbf)
294.5 s
Total Mass Flow Rate
1.15 kg/s (2.5 lbm/s)
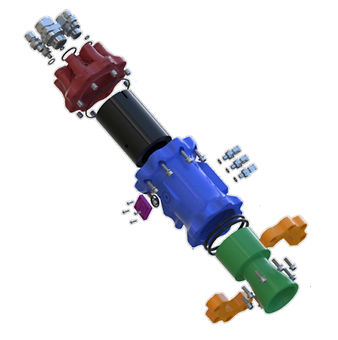
Exploded-View of Jessie Engine
Personal Responsibilities:
-
Support all aspects of the testing campaign (proof, leak, cold flow, etc.)
-
Review cold flow and static fire procedures
-
Prepare Hydra for cold flow and static fire testing
-
Operate the DAQ
-
Engine assembly and integration
-
Swaging, bending, and cutting tubes
-
Data analysis
-
Ox cleaning
-
Ensure proper PPE during all testing
-
Review and approve GD&T Drawings for hardware changes
-
System-wide troubleshooting
Jessie-Hydra Static-Fire 3
Play Video
Jessie Workhorse Engine Static-Fire 3 (3 seconds) at the Friends of Amateur Rocketry (FAR) in Mojave, California on November 17, 2018
First successful test of the engine, however a procedural error occurred and data was not recovered.
Jessie-Hydra Static-Fire 2
Play Video
Jessie Workhorse Engine Static-Fire 2 (6 seconds) at the Friends of Amateur Rocketry (FAR) in Mojave, California on August 4, 2018
Unsuccessful test of the engine due to incorrect cold flow setup. Resulted in highly fuel-rich combustion.
Jessie-Hydra Static-Fire 1
Play Video
Jessie Workhorse Engine Static-Fire 1 (6 seconds) at the Friends of Amateur Rocketry (FAR) in Mojave, California on June 2, 2018
Unsuccessful test of the engine due to poor startup timing sequence. Resulted in a hard start and damaged injector.
Preliminary Launch Vehicle Sizing
Preliminary Launch Vehicle Sizing
January 2019 - May 2019
As part of ASTE 574: Space Launch Vehicle Design at the University of Southern California (USC), individually conducted a preliminary sizing for a launch vehicle (LV) capable of delivering a communications satellite into a high inclination orbit for the Air Force.
Personal Responsibilities:
-
Technical report
-
Mission trajectory simulation on MATLAB
-
Design trade study for component selection (i.e. engines) to determine the smallest configuration
-
Layout and size all major systems needed at the smallest possible configuration (i.e. stages, propellant tanks, etc.)
-
Generate a "scale" 2D drawing of the launch vehicle
-
Calculate various parameters on all sub-sections of the launch vehicle (i.e. ground loads, flight loads, the center of masses, etc.)
-
Cost estimation using the U.S. Air Force Space Planner's Guide (1965) cost model

2D Scale Drawing of the Launch Vehicle
Material Selection Trade Study
September 2018 - December 2018
As part of MASC 583: Material Selection at the University of Southern California (USC), individually conducted a material selection trade study using CES EduPack to find a suitable replacement material for a graphite rocket nozzle that would axially crack during static fire tests.
NOTE: For more information regarding the engine, please refer to the "J&J ENGINES" section

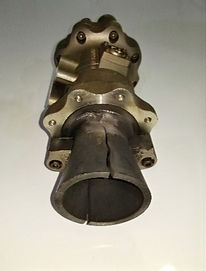
View of graphite nozzle cracking during Jessie Static-Fire 2 at the start-up phase
Personal Responsibilities:
-
Technical report
-
Layout material requirements based on the predicted engine performance parameters
-
Using CES EduPack, narrow down material choices from thousands to three ideal options by comparing various properties (modulus, density, melting point, etc.)
-
Conduct research on narrowed material choices for cost, applicable uses, and availability
-
Make a final selection from narrowed material choices based on data, research, and system compatibility
Material Selection Trade Study
Electomagnetic Longboard Braking System
Electromagnetic Longboard Braking System
May 2015 - August 2015


3D rendering of proposed custom longboard truck design that would house the electromagnet, rotating disk, batteries, etc. Due to time constraints and manufacturing limitations, the project was kept at a conceptual design with more focusing on feasibility testing.


Custom electromagnet that was used with the feasibility test rig.
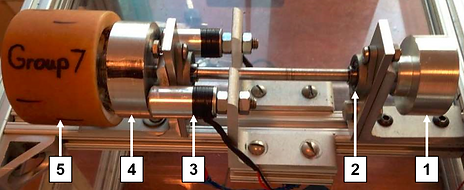
View of the apparatus mounted on top of the test rig. For a full view of the test rig, please refer to the final report attached.
-
Machined aluminum flywheel used to rev up the shaft/wheel using a motor to the desired RPM that equals 25 mph
-
Shaft aligned using ball bearing similar to those found on longboards
-
Two electromagnets to generate optimal drag
-
A conductive aluminum disk that generates eddy currents to induce a braking force on the longboard wheel
-
Longboard wheel connected to the aluminum disk
As part of MECH 650: Mechanical Capstone Project at the Wentworth Institute of Technology (WIT), my team and I created a concept proposal and conducted feasibility tests for an electromagnetic braking system that can be mounted onto standard longboard decks to increase rider safety. This was accomplished using the concept of eddy currents that induce a magnetic drag force on conductive metals rotating at high velocities.
Personal Responsibilities:
-
Technical report
-
Technical presentation
-
Project scope formulation
-
Background research
-
Concept design
-
SolidWorks modeling
-
Project scheduling
-
Team management
-
Test matrix
-
Test rig design, part procurement, and assembly
-
Progress reports
-
Design reviews with the project advisor
-
Data analysis
bottom of page